Does your company think of supply chain management and production scheduling as simply processes to convert orders into an executable manufacturing schedule? If so, it might be missing out on some of the greatest opportunities to improve on-time delivery, optimize inventory, and increase profitability. Over the years I’ve observed repeatedly how data helps companies eliminate conflicts, set priorities, and bring people together around shared objectives — when teams use data to optimize metrics across supply chain management and production scheduling, they create the greatest impact across the enterprise. The longstanding production scheduling – supply chain management balancing act is a common one among manufacturers, and for the last fifteen years I’ve had a front-line view of how world-class companies use data to overcome production-supply chain conflicts.
Data Fuels Decisions, Inventory Turns Just One Piece of the Data Puzzle
I love working at On Time Edge — it’s the most mentally stimulating job I've ever had, and there’s constantly something to learn. And I'm so grateful for our amazing clients, consultants, and technology partners. Not only are they among the very best in their fields, our conversations always offer new insights and wisdom. As one example, it's enlightening to hear supply chain experts explain how they make decisions, which metrics they use to evaluate success, and how they view manufacturing as a critical part of the supply chain.
For manufacturing companies that make to stock, one thing they consistently measure is inventory turns. It's a sign of how efficiently products move along a company's supply chain and an indicator to help the organization pinpoint a pace of sales so that items are neither obsolete nor perpetually out of stock. Ultimately, more inventory turns means lower cost to store it.
Metrics imbalance favors supply chain
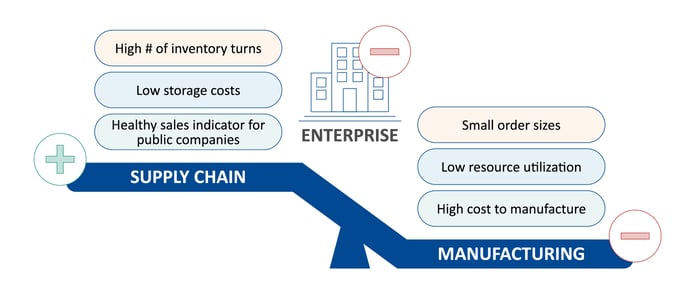
Metrics Can Create Conflicts Between Supply Chain Performance and the Production Schedule
More than one expert has pointed out that to achieve a high inventory turn score, it often requires the manufacturing plant to process smaller order sizes.
But wait — that's contradictory to what the people in manufacturing operations are trying to achieve.
Most plant managers want larger order sizes, which allow them to run the same product for a longer time. Long runtimes reduce the number of changeovers, and sometimes even shorten changeover time between product types — short product runs drive up machine downtime and waste operator time. The focus on long runtime also simplifies the process of managing and ordering the raw materials required for the production run and, to a degree, helps reduce shop floor operator training. For the shop floor, longer product runs mean higher operational efficiency.
Metrics imbalance favors manufacturing
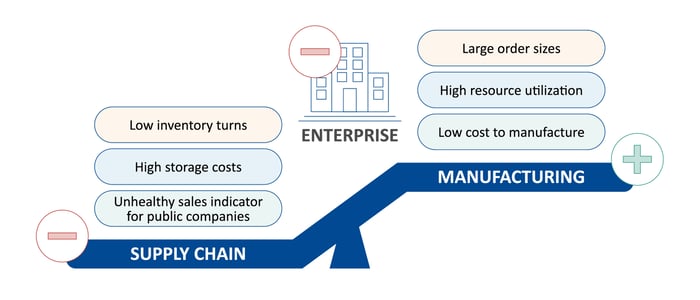
Their goals don’t align, so supply chain planners and the manufacturing plant are often working against each other. The plant works hard to reduce downtime with longer runs — resulting in more product on the shelf for long periods and fewer inventory turns. Supply chain planners are working just as diligently toward smaller order sizes to meet inventory turn goals — which affects plant efficiency and product cost.
Data is Critical for Setting Goals to Optimize Supply Chain and Production Schedule
Supply chain management experts have pointed out that data is the key to eliminate the conflict of goals between two groups critical for industrial organization success. World-class manufacturers combine supply chain data with manufacturing data to strike the perfect balance between inventory turns and order sizes.
Step 1 | Use Good Supply Chain Data
Precise supply chain data is a must-have to analyze the cost differences for different inventory turns. Typically this data resides in the company’s ERP system.
Step 2 | Capture the Right Manufacturing Data
Typically manufacturing efficiency data by order size is available in the manufacturing operations management (MOM) systems. More specifically, it’s in either a manufacturing execution system (MES) or an overall equipment effectiveness (OEE) tracking system. While these systems report utilization and efficiency metrics by order size and product SKU, they often require product costing data from the ERP system.
Step 3 | Analyze Cost Differences for Different Order Sizes
When manufacturing companies combine supply chain data with manufacturing data, they have the power to analyze costs for different order sizes. The result is insight to optimize order sizes and inventory turns. That sweet spot isn’t a magical number — it’s optimizing stock levels, inventory turns, and manufacturing costs. Of course, it's always going to be a compromise between the two disciplines — manufacturing and supply chain. But then, the exercise isn't about which team has better metrics; it's about helping the company win as each group has and hits the right targets.
Optimized metrics favors enterprise
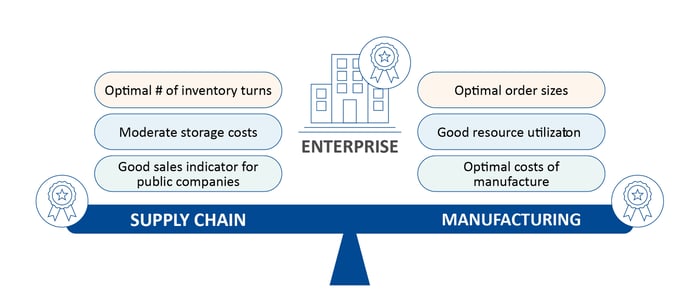
Foundational Questions to Eliminate Supply Chain Management – Production Scheduling Conflicts
If you’re a plant manager, production planner, or production scheduler, start by asking a few key questions like:
- Does the plant have an open and collaborative relationship with the supply chain management team?
- Do the supply chain planners have access to data from plant systems?
- Does the production scheduling software use the right models to optimize the production schedule?
- Are we collecting the right data and enough of it? How can we solve data gaps?
If you’re a supply chain planner or manager, start with these questions:
- Have we shared our analysis and data with the plant?
- Does the plant know how to apply supply chain data with data from their systems?
Everyone, especially executives at the corporate level, should be asking tough questions as well:
The answers to these questions don’t come easily, but simply by asking them companies position themselves for operational excellence and greater success.