Are manufacturers aware they have hidden production capacity? Companies that find and free up hidden production capacity can avoid costly equipment purchases, open the door for additional sales, or reduce the time and cost of existing production.
I’ve been a part of organizations that were struggling to satisfy customer demand — we simply could not produce enough product, or at least the right product at the right time. Determining how to resolve the issue would often put the operations engineering and production planning teams at odds. The solution most obvious to engineering was to continue running products in basically the same lot sizes, but at higher speeds. This approach required expensive new equipment. Besides the equipment purchase, there were other significant costs: inventory builds, downtime for installation, debug after installation, and operator training.
On the other hand, the production planning team wanted more flexibility. Their vision was to improve utilization of the existing equipment, to become nimbler and more flexible. This approach would enable the plant to run smaller lot sizes on a more frequent basis which shortens the time between replenishment of critical SKUs and reduces inventory.
As there are valid arguments for each approach, what is needed to make an informed decision? Every manufacturing organization can take three steps to uncover hidden production capacity.
Step 1: Find the True Production Capacity of Existing Equipment
Step 2: Decide Where to Focus to Reduce Downtime
Step 3: Ask if Existing Capacity is Enough to Meet Customer Demand
Step 1: Find the True Production Capacity of Existing Equipment
The first step to determine what’s truly possible is to express the overall capacity of the existing equipment, then to show how much of that capacity is used productively. A waterfall diagram is a great tool for this. It shows theoretical capacity (without any losses) and how much capacity is lost to categories such as changeovers, planned shutdowns, and breakdowns.
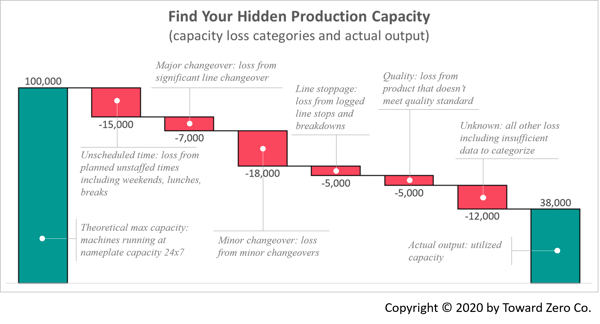
(download and use the hidden production capacity analysis spreadsheet shown above)
A waterfall loss diagram is only as good as the data available. An organization that doesn’t have an automated OEE system will need to use manually collected data, and hope that the data is directionally correct. Companies with an automated OEE system have a much more accurate understanding of downtime losses and can break the data into more granular categories.
Step 2: Decide Where to Focus to Reduce Downtime
Once you have the total capacity and downtime data, it’s time to determine what’s possible. Where can you improve, and by how much? This is when cross-functional groups must put their heads together and agree where to focus and apply the Continuous Improvement process. This is where the real work starts! Simply having the data doesn’t fix anything, we must act.
In the case of one company I worked for, the data showed that minor changeovers were the largest source of loss. Previously we had focused on major changeovers as they took four times longer than the minor changeovers. Better insight showed us we needed to change our focus. Our team immediately started implementing Lean quick changeover methodologies and we cut loss from minor changeover by over 50% — this was fun! After that improvement, the team focused on the next largest opportunities, which was the major changeovers and improving information in the “unknown” category by implementing an OEE system. The continuous improvement cycle continues over and over.
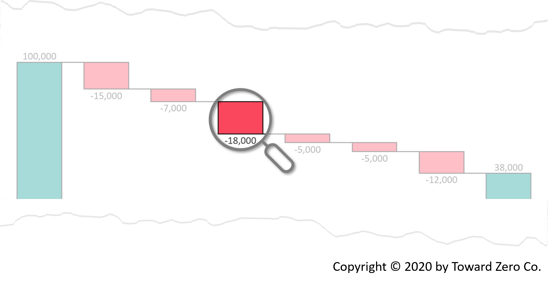
Step 3: Ask if Existing Capacity is Enough to Meet Customer Demand
The company should examine the fresh capacity data and challenge assumptions about the old ways of operating. Often a fresh set of eyes from outside the organization is helpful to burst through paradigms. Once the team agrees to how much capacity it can make available, they should work with the supply chain group to determine if the opened up capacity is enough to meet customer needs. With typical OEE around 50%, I believe most companies have plenty of capacity; unfortunately, they usually don’t know it.
Getting Started to Uncover Hidden Production Capacity
If your company is thinking about adding equipment to boost manufacturing production capacity, it should make analyzing hidden production capacity a priority before making any purchase. Active engagement throughout the organization can help your company make well-informed decisions about investments and priorities. Keep in mind these learnings from other organizations that have successfully uncovered hidden production capacity:
- Many companies are not aware of their true capacity
- Improving capacity utilization requires an aligned cross-functional team
- OEE systems provide valuable insight