There are many well-documented benefits of digital factory and paperless quality initiatives for manufacturing plants. A paperless quality system reduces costs, facilitates faster implementation of changes, provides tighter change management control, and makes quality data available for reporting and analytics systems. Ultimately, paperless quality is already a large part of the Industry 4.0 value proposition. As technology costs continue to drop, companies are prioritizing paperless quality initiatives. However, many organizations struggle to migrate from their existing system to paperless quality in manufacturing.
With so many benefits, why do manufacturers struggle to migrate to a digital system? More importantly, how can a company put paperless quality in place successfully?
Going Digital in Quality: Focus on Quality Processes First
When starting your digital quality journey, the critical first step is to optimize quality processes and procedures before you digitize them. The more optimized the procedures become the less time and money required to create the digital versions.
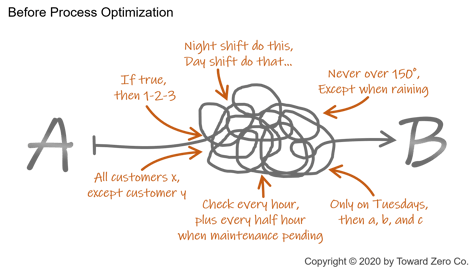
Let’s explore what we mean when we use the word optimize:
- Take a look at all the quality processes already in place. Are there some elements of quality procedures or even full procedures that the company can describe and implement the same way, even for different products or locations in the manufacturing value stream?
- Are there any steps in the existing process that are not required that the organization can eliminate?
- Can any of the data being manually collected today be recorded automatically by an existing OEE system, manufacturing operations management system (MOM), or quality management system (QMS)?
- Can the MOM or QMS capture the inspector’s data automatically with either a login or a badge scan?
- Is there any other data that is critical to quality that can be collected automatically, such as ambient temperature or humidity from the building management system (BMS)?
If the organization can optimize processes with standard sections, many paperless quality tools can capture them for teams to reuse. This approach reduces system setup time and makes it easier to manage change to these standard sections across all the quality processes that use them.

One example is a standard header with SKU, product name, operation number, inspection location, and inspection team member information. The organization can use a standard header for all quality procedures.
Another example is a standard inspection or measurement that yields a single quality value. This inspection component could be used just once in a procedure or multiple times, with just the product variable changing with each inspection.
Standardization is a Key Element to Going Digital in Quality
Now that you have optimized your processes, is there an opportunity to standardize as well? Are there multiple plants producing the same or similar products that can use the same process? Often with paper-based processes, small incremental changes happen over time, resulting in processes that are slightly different from plant to plant (and sometimes between different areas in the same plant). Standardizing reduces the time to implement a paperless quality system.
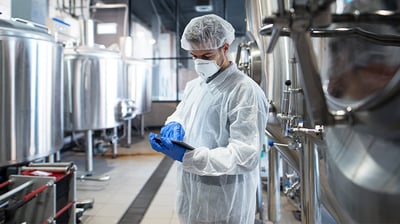
Some team members may resist process changes. If you expect resistance, it might be beneficial to standardize the manual process first to give team members time to acclimate to the change before implementing the digital system. This approach reduces the risk that team members blame the process change on the electronic system. Instead, teams have time to acclimate to the modified quality process, and the transition to a digital system only means a change of interface and documentation experience, not of the process itself. While this method increases the time and effort required for the transition to a paperless quality system, it supports adoption and reduces initiative risk.
Paperless Quality like any Change is a Journey, Not an Event
It’s unrealistic to think that a company can migrate every manual quality process to a paperless system in one project. Often the list of processes is long, and the value diminishes some less-used processes. Instead of trying to convert every process, focus on quick wins. Prioritize quality processes based on how often teams use them, how optimized they are, and how standardized they are across the enterprise.
By focusing on a subset of quality processes, the organization can achieve results quickly, and the results will have a quicker impact on the cost of goods sold (COGS). This focus also reduces the training and change management requirements, increasing adoption and overall program success.
Getting Started with Paperless Quality in Manufacturing
A purposeful approach to migrate from manual quality processes to paperless quality in manufacturing can lead to program success. Digitalization is not the goal, however. Manufacturing organizations should be driving toward corporate goals which may include accelerating performance improvement, reducing costs, and other strategic objectives.
These early steps can have a powerful impact on your company’s ability to execute paperless quality quickly and effectively:
- Work cross-functionally. Enlist help and buy-in across functional roles. Even though the focus is “quality,” shop floor operators, maintenance engineers, IT leaders, and others are essential to the effort.
- Apply proven best practices. Looking outside your company’s four walls for best practices, recommendations, and objective advice can help your organization avoid pitfalls that might not be obvious with a close-up view.
- Zero in on quick-win, high-impact improvements. Making the switch from manual to paperless quality processes is a journey. Early wins will fuel buy-in, adoption, and even senior leadership enthusiasm. If optimizing a subset of processes can save the organization notable time or cost, it paves the way for building on that win by going digital.