Manufacturers serious about improving OEE need to invest in automated data collection. Though the intention of manual data collection is good, this approach doesn’t provide real-time insight or the level of accuracy and detail that an automated data collection can produce. Perhaps more importantly, automated data collection helps you shift employees’ attention to high-value work like running machines and solving problems that hinder operational performance.
“It’s a sign of respect to give employees meaningful work” is a common theme among Lean practitioners. I assert that manual downtime collection is most often not meaningful work and in fact can be a de-motivating task for employees. This is unfortunate, as the intention is good — if no one understands downtime, the company can’t properly address it. At best, manual downtime collection paints a high-level picture and provides rudimentary data. At its worst, it can create a very misleading perception of how equipment is performing.
Manual Data Collection is no Easy Task
When there’s no automated data collection, companies rely on manual processes, sometimes using a paper log. This method is cumbersome and does not provide the data required to improve OEE.
- Operations management usually assigns the task of downtime tracking to the line lead — the same person responsible for ensuring the team resolves downtime issues. That individual is very focused on getting the line running, downtime logging happens after the fact and is often overlooked.
- Some lines or manufacturing cells are physically long and contain multiple visual obstructions, which can make it difficult to observe the root cause of a stop.
- A production line might have dozens of short stops (one minute or less) throughout a shift; this makes logging minor downtime a tedious and unrealistic task.
Reporting Process is Archaic, Time-Consuming
Since manual data collection is tedious (and often provides little value), I have seen many instances of “pencil whipping” the downtime report at the end of the shift. In this scenario, the experienced line lead reviews the shift output and does some mental math to determine how many minutes of downtime needs to be accounted for. He then thinks back about the issues during the shift and distributes the requisite minutes of downtime in the log. While manual data collection is a poor use of time for one of the most valuable employees in the plant, the exercise is rendered useless because it is not based on solid evidence and not taken seriously.
Making things worse, the input isn’t a good foundation for analysis or improvement. The most rudimentary manual systems log downtime on paper at the production line, and slightly more sophisticated methods go into a shared drive. Manually collected data is often handed over to someone in an administrative role who then manipulates it into a usable format. It’s one more time-consuming activity that doesn’t provide real-time insight.
Are Reported Facts Hiding Reality? (or, Your Line Doesn’t Really Run Like That)
These and other pitfalls associated with manual data collection mean that operations leaders and continuous improvement specialists don’t have accurate insight regarding production rates.
Manual downtime tracking implies few downtime occurrences throughout a shift, and further provides no information about line slowdowns, post-changeover ramp-up timing, or other performance erosion. It creates an inaccurate perception of uptime and downtime — in reality, the line isn’t as stable as the data indicates.
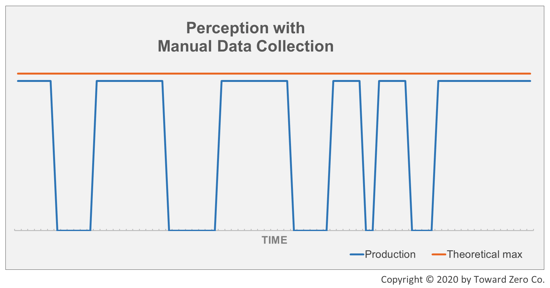
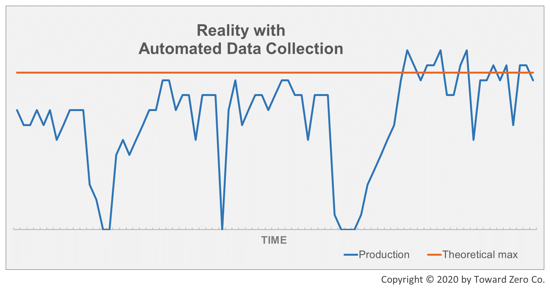
Automated data collection reveals much more instability and that the production line has:
- Significantly more downtime events
- Inconsistency in changeover times
- Run rates higher than what everyone thinks is the maximum line run rate
- Run rate variation across the same SKU family
- Extended ramp-up times after changeovers
Ultimately, manual data collection isn’t worth the paper used to capture it.
Good News: Cost of Automated Data Collection Way Down
The cost to implement an automated OEE system has decreased significantly over the years. Manufacturers have pushed machine OEMs to produce equipment that provides productivity data. In addition, many now provide adapters for older machines. Even without built-in connectivity, inexpensive data collection devices can be installed to provide the signals required for automatic OEE data collection.
On the OEE platform side, off-the-shelf systems now come with substantial “out of the box” functionality, eliminating the need for custom programming. All of this is good news — manufacturing companies can expect faster implementation and much less capital investment than just a few years ago. In addition, this investment can support other initiatives such as predictive quality or predictive maintenance, making the investment even more valuable to the organization.
Simple Steps to Justify Automated Data Collection
The first step for any organization with manual data collection OEE tracking is have frank conversations to understand how much stock the team puts in the existing data. The next step is to determine the business benefit of improving capacity utilization — articulate the value in terms of increased revenue or decreased costs, what can you achieve as you free up capacity?
- Increase production volume to achieve $_____ more in product sales
- Reduce manufacturing overtime by $_____
- Save $_____ by insourcing product from contract manufacturing
- Reduce lot sizes to reduce finished goods inventory by $_____
There are countless case studies from many industries to help justify automated data collection and they almost always show how:
- Manual data collection can never deliver a real-time, accurate picture of performance
- Manual data collection is an unnecessary frustration to employees
- The cost and speed of automated data collection and automated OEE systems have decreased significantly over the years
If your company has delayed automated data collection, find out why. Then gather your analysis and the team to show how automated data collection supports achieving business goals. Everyone — from your line leaders all the way to the CEO — will thank you for driving the business to automated data collection which is foundational for OEE improvement.